Zf Vt1f Cvt Repair Manual
May 22, 2012 - ZF GETRIEBE N.V. SINT-TRUIDEN Description Automatic Gearbox VT1F Davy. Description Transmission VT1F Page 21 of 312.2 ValvesThe CVT is co. In the Manual/Sport position, the car will move forwards in CVT sport mode. This can cause some problems when braking on a slippery surface,. Zf Vt1f Mini - Download as PDF File (.pdf), Text File (.txt) or read online. ZF6hP26 Repair Manual. Transmission Basic Principles of Continuously Variable Transmission Shift Positions Functionality in Park and Neutral Normal.
Zf vt1f gearboxdescription. 1.
ZF GETRIEBE N.V. SINT-TRUIDEN Description Automatic Gearbox VT1F Davy Geuns June 2003. Table of contentsI. General Description VT1F 4 1. Introduction 4 2. Conventional Autom.
Transmission vs. Continuously Var. Transmission 6 3. Basic Principles of Continuously Variable Transmission 7 4. Shift Positions 8 5.
Functionality in Park and Neutral 9 6. Normal Operation 9 7. Transmission Communication 10 8. Related Car Components 10 8.1 Centre Controle LEDs 10 8.2 Instument Cluster Display 10 8.3 Selector Lever Mechanics 10 8.4 Torsional Damper 11 9. Towing of the Vehicle 11 10.
Drain and Refill 11II. Transmission Layout 12 1. Group One – Mechanical Torque Flow 13 1.1 Planetary Gear Set 13 1.2 Multiplate clutches 14 1.3 Pulley and Steel Belt 15 1.4 Pinion Shaft 16 1.5 Differential 16 1.6 Mechanical Operation 17 1.6.1 Selector Lever in the Park or Neutral Position 17 1.6.2 Selector Lever in the Drive Position 18 1.6.3 Selector Lever in the Reverse Position 19 2.
Group Two – Control System 20 2.1 Oil Pump 20 2.2 Valves 21 2.3 Pitot system 21 2.4 Sensing Shoe 22 2.5 Oil Temperature Sensor 22 3. Group Three – External Connections 23 3.1 Park / Neutral Switch 23 3.2 Oil Cooler Locations 24 3.3 Transmission Secondary Speed Sensor 25 3.4 Selector Shaft 26 3.5 Connector 26III. Strategies 27 1. Behaviour in Specific Situations 27 1.1 Idle when Drive is Selected 27. 1.2 Take Off / Pulling Away 27 1.3 Light Throttle Acceleration in Drive or Sport 27 1.4 Kick Down in Drive or Sport 28 1.5 Emergency Stop 28 1.6 Reverse Running 28 1.7 Fault Mode 28 2. CVT Software 29 3.
Transmission Reset and Reference 30IV. Adaptation Procedures 31. Description Transmission VT1F Page 4 of 31Automatic Gearbox – VT1F Fig. 1: Gearbox and selector mechanismI. General description VT1F1. IntroductionThe stepless shifting pattern of the transmission provides a very comfortable drive, as well ashaving full vehicle performance, available at any time. Description Transmission VT1F Page 5 of 31The advantages of using an automatic transmission of this type are:- Low engine revolutions at constant speeds.- Improved emission control/fuel consumption.- Low noise, vibration and harshness levels.- Smooth acceleration.- Flexible driving on mountain roads.
2: CVT box Fig. 3: Bell Housing.
Description Transmission VT1F Page 6 of 312. Conventional Automatic Transmission vs. Continuously Variable Transmission.In the figure below the variograms of a hand shifted or normal automatic transmission and theCVT are compared with each other. With the conventional automatic transmission, maximum6 ratio’s (gears) are available, but mostly even less. When the transmission upshifts, it has tofollow the bold or dotted lines of the first image depending of the amount of throttle. With theCVT, the whole range of ratios between the Low and the Overdrive lines is available forshifting as shown in the second image.The shift point of both transmissions is related to the amount of throttle. As more throttle isapplied, the transmission upshifts at a higher engine speed.
With the conventionaltransmission it is clear that the engine speed drops back when shifting to a higher gear. This isnot the case with the CVT. The CVT will upshift at a constant engine speed, by moving thepulleys as explained in the next part.
However, alternative shifting strategies are also possible.This can help to create a quicker acceptance by new CVT drivers. 4: Variogram 4 step automatic transmission and CVT Transmission. Description Transmission VT1F Page 7 of 313. Basic Principles of Continuously Variable Transmission 1 Input from the engine 2 Output to the wheels 3 Drive pulley at minimum diameter (Low) 4 Driven pulley at maximum diameter (Low) Fig. 5: Pulleys in low position 1 Input from the engine 2 Output to the wheels 3 Drive pulley at maximum diameter (overdrive) 4 Driven pulley at minimum diameter (overdrive) Fig. 6: Pulley positions in high ratio (overdrive)Unlike conventional planetary automatic transmissions that provide a limited number of gearratios, usually four, five or six, the CVT, as its name suggests, continuously varies the gearratio. A low gear (low ratio) makes it easier to pull away from a rest position, the drive pulleydiameter being relatively small, while the driven pulley diameter is large by comparison.
Thedrive belt is used to transmit power and torque. As acceleration takes place it becomespossible to select a higher ratio by increasing the diameter of the drive pulley while, at thesame time, decreasing the diameter of the driven pulley.
© 2013 Sears Brands, LLC. Discount will be automatically applied during check-out. Sears Holdings reserves the right to terminate or modify this offer at any time for failure to comply with its terms and/or due to any operational malfunction of the software, hardware or equipment required to process this offer. May not be used with any other coupon, associate discount, or during Family & Friends or Member events. Ducane cmpb furnace manual.
This degree of change can becontrolled to ensure that the most suitable ratio is provided.The CVT uses a primary pulley and a secondary pulley. Both pulleys have one fixed half andone mobile half, controlled by hydraulic pressure. The position of the drive belt on the pulleyswill determine the ratio. If the mobile half of the pulley is close to its opposite half then thedrive belt is forced to travel around the outer circumference. When the pulley is open widethen this circumference is reduced. The primary and secondary pulley mobile halves are.
Description Transmission VT1F Page 8 of 31diagonally opposed so when the drive belt diameter is reduced on the primary pulley, itincreases on the secondary pulley.To pull away, a low ratio is required. To provide this, the primary pulley is open, allowing thedrive belt to sit down into the pulley and forcing it to run around the outer of the closedsecondary pulley. As vehicle speed increases, a higher gear ratio is required. To do this, theprimary pulley gradually moves towards its fixed partner, increasing the pulleycircumference. At the same time the secondary pulley is forced apart reducing pulleydiameter, therefore creating a higher gear ratio. An overdrive ratio is obtained when theprimary pulley is fully closed and the secondary pulley is fully open. The secondary pulley isnow forced to rotate approximately two and a half time for every turn of the primary pulley.4.
Shift Positions.Possible shift positions for the VT1F are Park, Reverse, Neutral, Drive and Sport/Manualposition (other shifter lay outs are also possible of course, for instance with an L position).In the Drive position, the car will move forwards in standard CVT mode. The engine speedwill be limited to approximately 4500 rpm unless kick down is used by fully depressing thethrottle pedal when the engine speed will rise to approximately 5500 rpm. Of course othercalibrations are also possible.In the Manual/Sport position, the car will move forwards in CVT sport mode. The enginespeed will be limited to approximately 5000 rpm unless kick down is used by fully depressingthe throttle pedal when the engine speed will rise to approximately 5500 rpm. Again, othercalibrations are also possible.
Illuminated gear position 2. Gear selector lever Fig. 7: VT1F gear lever & M+ /-In Sport position the transmission will be tuned in a different way than in Drive mode.
Zf Vt1f Cvt Repair Manual Pdf
Thetransmission will upshift at a higher engine speed, providing more sportive driving. The Sportdriving calibration is designed to be more responsive to driver command, but will be lessrefined than the D position. Description Transmission VT1F Page 9 of 31If the gear shift lever is moved into the ‘Plus’ or ‘Minus’ position from Manual/Sport, thesystem will change into Manual mode. The transmission then works with 6 (or more) “gear”ratios. The system will select a gear appropriate to road and driving conditions. To change upa gear, the driver must move the gear lever to the ‘Plus’ position.
To change down, the drivermust move the gear lever to the ‘Minus’ position.If the CVT software decides that a shift might cause damage to the transmission, such asattempting to shift to 1st gear at 100 km/h, the gear change will be prevented. If the driverdoes not shift up, the next gear will be automatically selected when the engine revolutionsreach approximately 6000 rpm. Equally, if the driver does not shift down when reducingvehicle speed, the system performs the down-change automatically thus ensuring thetransmission is in the appropriate gear.5. Functionality in Park and NeutralThe engine can only be started in Neutral or Park, as with any automatic transmission.A spring and cone operated pawl mechanically locks the secondary pulley when the selectorlever is moved to the Park position. If the lever is set in the Park position when the vehiclehas a higher speed, the pawl will rattle without engaging Park. It will not engage until thevehicle speed drops below approximately 5 km/h.
Parking pawl 2. Secondary pulley Fig. 8: Parking lock6. Normal OperationThe operation of the transmission, during driving, has no comparison with that of aconventional automatic transmission. All kinds of tunings are possible. A possible tuning isthat if the accelerator pedal is depressed sharply, the engine rpm will rise considerably morethan in relation to the speed of the vehicle. This functionality is normal for a CVT but maysurprise drivers not familiar with this type of transmission.
Other tunings / variograms arealso possible, for example tunings that are closer to that of a conventional automatictransmission. Description Transmission VT1F Page 10 of 317. Transmission CommunicationThe VT1F has electronic components to control the gear ratios, the clamping force on the beltand the clutch pressure. The location of the components that form the steptronic transmissionvary depending upon vehicle installation.There are different options for the position of electronic components in the transmission. Forexample, the control methods associated with the transmission can be run as part of thesoftware in the ECU. The CVT software in the ECU receives inputs from the main sensors ofthis system, communicates with the gearbox interface unit (GIU) to control the transmission,accepts driver inputs and provides information to the driver via the instrument cluster. Withthis example the software is located in the ECU, while the drivers are in the Gearbox InterfaceUnit (GIU).
It is also possible to put both the software and the drivers in a TCU.8. Related Car Components 8.1 Centre Console LEDsThe configuration of which controle LEDs are to be used depends on customer. 8.2 Instrument Cluster DisplayThe same is valid for this part. The Instrument Cluster Display is also defined by thecustomer. 8.3 Selector Lever MechanicsPark, Reverse, Neutral and Drive SwitchesThe configuration of the selector lever is customer specific.
A shift lock (as in the picturebelow) must be integrated in the mechanism, to provide an idiot start protection. Gear selector lever 2. Gear selector lever detent 3.
Shift lock 4. Gear change selector rod Fig. 9: VT1F selector lever mechanism. Description Transmission VT1F Page 11 of 31 8.4 Torsional damperThe engine is connected to the input shaft in the transmission, via a torsional damper, insteadof the torque converter used by more conventional automatic transmissions.This torsional damper is not a part of the transmission. Drive plate gearbox side 2. Engine side Fig. 10: Torsional damper9.
Towing of the VehicleThe VT1F transmission must not be towed. This is because there is no oil pressure in theprimary pulley unless the engine is running and belt slip would therefore occur. Recoverymust be conducted with the front wheels lifted clear of the ground (suspended tow).With a manual transmission it still is possible to start the car by pushing or towing. This is notpossible with the CVT because there will be no oil pressure (as the engine and the pump arenot running) meaning that both clutches are disengaged and that there is no connectionbetween the engine and wheels.10. Drain & RefillA refill of the transmission oil is necessary every 45.000 km.For this purpose, the gearbox is equipped with an oil drain plug and a top filler plug. Description Transmission VT1F Page 12 of 31II. Transmission Layout Fig.
11: VT1F transmission Layout. Description Transmission VT1F Page 13 of 31The VT1F consists of a number of elements that can be divided into three groups, dependingupon their function.Group One – Mechanical Torque FlowElements providing the mechanical torque flow through the transmission.Group Two – Control systemThese elements relate to the control system. This system enables the transmission to transmitpower and to vary the ratio in a proper way, according to load conditions and driver demand.Group Three – External ConnectionsA number of elements have external connections with the transmission. Some of theseelements are either inside the gearbox, or immediately connected to it. Others can be part ofthe system, but can be located elsewhere on the vehicle.1.
Group One - Mechanical Torque Flow1.1 Planetary Gear SetThe planetary gear set enables the transmission to provide a drive torque in two directions,forward and reverse. Engine torque always enters the transmission through the input shaft ofthe planet carrier. This carrier can be directly connected to the sun-wheel by closing theforward multi-plate clutches. When it does, the epicyclic gear set rotates as one unit, andengine torque is transmitted directly to the primary pulley. The planet gears do not transmitany torque, therefore no mechanical loss will occur in the planetary gear set and the primarypulley will rotate in the same direction as the engine. This is the forward drive mode.
12: Planet gearsIn reverse mode, the annulus of the planetary gear set is held stationary by closing the reversemulti-plate clutches. Three pairs of planet gears are driven by the planet carrier, forcing thesun-wheel to rotate in the opposite direction.
Description Transmission VT1F Page 14 of 31 1. Planet gears 2. Input shaft 3. Annular gear Fig. 13: Planet gearsThere is a small multiplication of torque being transmitted since the ratio of the epicyclic gearset is 1:1.1, in order to compensate for frictional losses within the planetary gear set itself.1.2 Multiplate clutches.There are two Multiplate wet clutch packs; one forward and one reverse.
Zf Vt1f Cvt Repair Manual
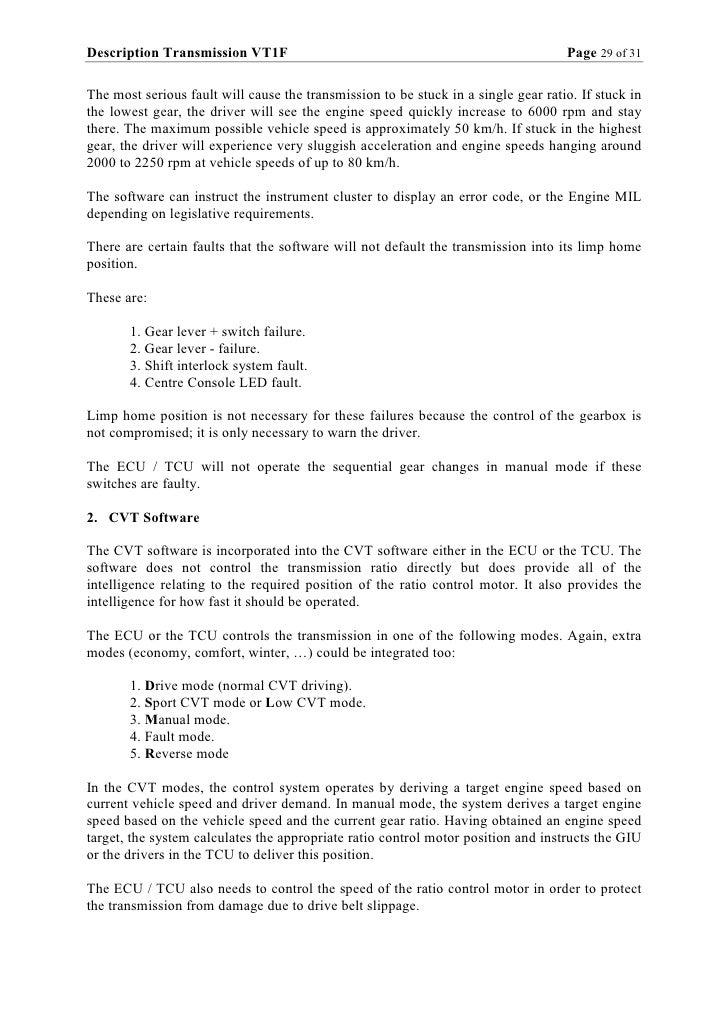
Each pack has threefriction plates providing six friction surfaces. The hydraulic pressure controls the clutches toallow the vehicle to move away smoothly by every throttle opening. By controlling the beltslip it also allows the vehicle to be held stationary after the drive gear is engaged. Oil from theoil cooler is directed to the clutch plates to prevent overheating of the friction surfaces. Forward clutch pack 2.
Reverse clutch pack Fig. 14: Planetary gear set showing clutch plates. Description Transmission VT1F Page 15 of 311.3 Pulley and Steel BeltThe main design feature of the CVT is a pair of steel 'V ' shaped pulleys connected by a steeldrive belt. The distance between centres of the primary and secondary pulley is 155 mm. Eachpulley consists of one fixed half and one axially slideable half, both having 11 degree slopingsides. The proven 24 mm wide 'Van Doorne' push type drive belt is used to transfer torquebetween the pulleys (applications for higher torque values can make use of a 30 mm drivebelt). The belt is lubricated and cooled by an oil jet from a nozzle.
Both moving halves aresituated diagonally opposite to each other in order to reduce misalignment of the drive beltduring shifting. Each moving half is connected to a hydraulic cylinder/piston. Hydraulicpressure is controlled by the control system, described in the section titled ‘Hydraulicsystem’. Ball splines prevent the moving halves from rotating relatively to their fixedpartners.
15: Steel Drive beltTorque transmitted by the planetary gear set acts directly onto the primary pulley, as the sun-wheel is splined to it. The steel drive belt transmits the power from the primary pulley to thesecondary pulley and the power from the secondary pulley is then transmitted to the pinionshaft.Torque and speed of the secondary pulley are determined by the position of the drive belt.The sizes of the two pulleys are designed to provide a range of ratios from 2.416:1 to 0.443:1resulting in a ratio spread of 5.45. The high overdrive ratio is particularly advantageous inrespect to fuel consumption.The steel drive belt has approximately 450 segments and is held together by 24 steel bands,12 on each side. All the segments are of the same thickness. Steel bands 2. Steel segments Fig.
16: Drive belt. Description Transmission VT1F Page 16 of 311.4 Pinion ShaftThe pinion shaft creates a two-set helical gear reduction between the secondary pulley and thedifferential. In this way, the rotational direction of the drive shafts will be correct.
Thereduction between the secondary pulley and the drive shafts can be made large enough to givegood vehicle performance. The pinion shaft is supported by two conical bearings, one in theclutch housing and one in a separate bearing support. Primary shaft drive gear 2. Differential crown wheel 3.
Pinion drive gear 4. Transfer gear pinion shaft 5.
Secondary shaft drive gear Fig. 17: Crown wheel & pinion1.5 DifferentialDrive torque on the crown wheel is transmitted to the vehicle wheels via a bevel geardifferential, just as in a manual transmission. The crown wheel is bolted to the differentialcase with 8 bolts.
The drive shafts are fitted to the differential with conventional CV jointsand seals. Conical bearings are used to support the differential. Differential bearing 2. Differential casing 3. Differential cross shaft 4.
Differential planet gears 5. Differential crown wheel Fig.